Chapter 2 - Design using flexures
Chapter 3 - Design for static stiffness
T-Flex-LC: A flexure-based hexapod with a simplified kinematic structure
Introduction
Hexapod manipulators have six arms that provide motion in six degrees of freedom. The arms consist of several links and joints. Commonly used joints are the revolute (R), universal (U), spherical (S) and prismatic type (P). Various combinations of links and joints can provide the six degree of freedom hexapod motion, such as the so-called 6PUS, 6RUS and 6UPS kinematic chains [1–3]. In a hexapod design, the components that perform the kinematic function of these joints can be traditional sliding- or rolling-contact components. Alternatively, when the application requires a high degree of determinism, flexure-based components can be used. Various flexure-based components have already been developed; they often comprise an assembly of multiple elastic components, such as leafsprings, notch hinges and wire flexures.
Principle
A new simplified kinematic design for flexure-based for hexapods with a kinematic chain that contains a universal joint in series with either a prismatic or a revolute joint (6PUS, 6RUS, 6UPS, 6URS) is presented. The novelty lies in the use of a single leafspring to replace the U-joint in series with either the P- or the R-joint as shown in Figure 1 [4-6]. This means that each of the six arms requires only a single leafspring and one spherical joint. Benefits of this design are a reduced part count, because conventional implementations tend to use a multitude of elastic components per kinematic joint. Associated advantages are the low cost, easy assembly and easy manufacture.
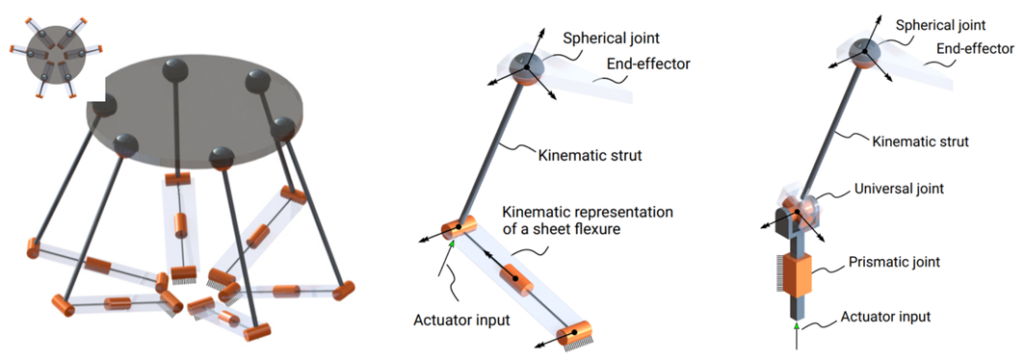
Figure 1. Left: schematic representation of new hexapod design, showing six arms with each a single
leafspring and a spherical joint. Center: single arm of the new design. Right: for comparison, a conventional arm of a 6PUS hexapod.
Physical demonstrator
A demonstrator for the proposed flexure design has been designed, built and optimized using the flexible multibody software SPACAR. The demonstrator has a layout that favors a high vertical support stiffness. For a payload of 15 N,
the stress in the flexures (stainless tool steel Stavax ESR) stays below the fatigue limit. Figure 2 shows a photograph of the demonstrator in the lab. Sensing is carried out by six magnetic encoders (RLS LA11, 0.244 μm resolution).
Actuation is provided by six custom built moving magnet actuators. Measurements of the workspace, maximum
velocity, maximum acceleration and repeatability have been performed, see Table 1. The range of motion listed is for simultaneous rotations and translations. The repeatability has been measured with a capacitive sensor (Lion
Precision CPL290). The bidirectional repeatability, as defined in [7], for a vertical displacement is 0.50 μm with a 15 N payload. It reduces to 0.38 μm when filtered for floor vibrations.
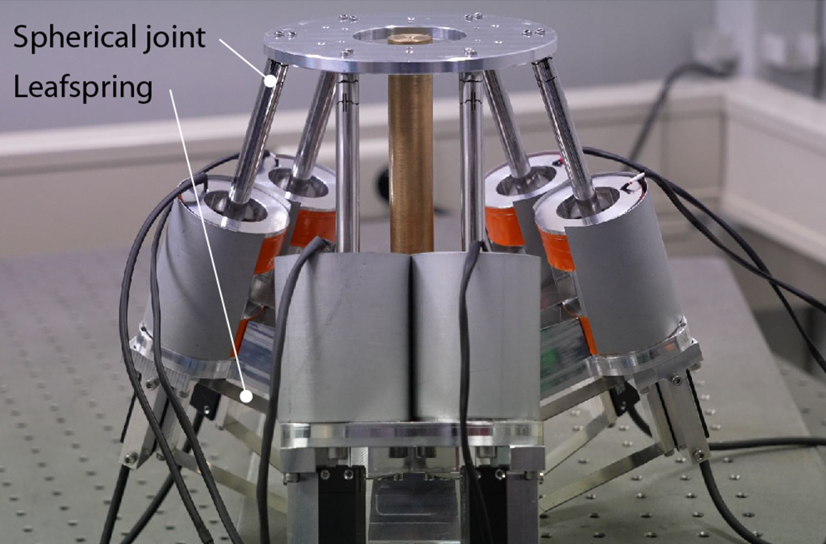
Figure 2. Photograph of the T-Flex-LC with proposed flexure design.
Table 1. Measurements on the physical demonstrator.
Range of motion (rot.) | -2 to +2 deg |
Range of motion (transl.) | -3 to +3 mm |
Max. velocity (transl.) | 100 mm/s |
Max. acceleration (transl.) | >500 mm/s2 |
Repeatability (bidirectional vertical displ.) | 0.38 μm |
Footprint (base diameter) | 295 mm |
Height | 250 mm |
Stiffness (vertical, simulated) | 20 N/μm |
Discussion
While the new kinematic design of the hexapod arm has the benefits of simple elastic components, it makes actuation and sensing more challenging: the sensor and actuator need to accommodate some off-axis motions. For this reason, a custom moving magnet actuator with a fairly large air gap of 5 mm was designed, at the expense of increased heat production (though located at the fixed base). Depending on the desired end-effector range of motion, magnetic encoders may provide insufficient misalignment tolerance; contactless triangulation laser displacement sensors, albeit more expensive, could provide a solution.
Developed by University of Twente
- Tim Koers, Marijn Nijenhuis, Dannis Brouwer
References
[1] Fazenda N, Lubrano E, Rossopoulos S, Clavel R. Calibration of the 6 DOF High-Precision Flexure Parallel Robot “Sigma 6”. In: Parallel Kinematic Machines in Research and Practice. Chemnitz, Fraunhofer; 2006. p. 379–98.
[2] Timmer Arends JH, Voss KHJ, Hakvoort, WBJ, Aarts RGKM. Kinematic Calibration of a Six DOF Flexure-based Parallel Manipulator. In: ECCOMAS Thematic Conference on Multibody Dynamics. Prague; 2017. p. 199–211.
[3] Physik Instrumente. H-860 6-axis motion hexapod. Cited 2023 May. http://www.pi.ws/
[4] Koers, T. M. (2023). Design of a redimensionable and economic flexure-based 6-DOF manipulator demonstrator, EngD Thesis, University of Twente. https://research.utwente.nl/en/publications/design-of-a-redimensionable-and-economic-flexure-based-6-dof-mani
[5] Brouwer DM, Koers TM, Nijenhuis M, Actuated Leafspring Hexapod, Patent request submitted N2034815.
[6] Tim. M. Koers, Marijn Nijenhuis, Dannis M. Brouwer, T-Flex LC: A flexure-based hexapod with a simplified kinematic structure, ASPE annual conference proceedings, Nov 2023.
[7] Grabowski A, Diez P, Schulze B. This Is How PI Does Measuring – Part II. WP4032E; 2020. Cited 2023 May. http://www.pi.ws/